Distributed Temperature Sensing – DTS
Security, Technology 2024-11-29
Distributed Temperature Sensing System
Distributed temperature sensing systems (DTS) are fiber optic based optoelectronic instruments which measure temperature along the length of the fiber optic sensing cable. The unique feature of a distributed temperature sensing system is that it provides a continuous (or distributed) temperature profile along the length of the sensing cable and not at discrete sensing points which must be pre-determined.
Fiber Optic Temperature Sensor How It Works
DTS systems contain a pulsed laser which sends in an approximately 1m pulse (equivalent to a 10ns time) into the fibre optic. As the pulse travels along the length of the fiber optic, it interacts with the glass. Due to small imperfections in the glass, a tiny amount of the original laser pulse is reflected back to towards the DTS sensing system. By analysing the reflected light the DTS is able to calculate the temperature of the event (by analysing the power of the reflected light) and also the location of the event (by measuring the time it takes the backscattered light to return) to typically within a metre.
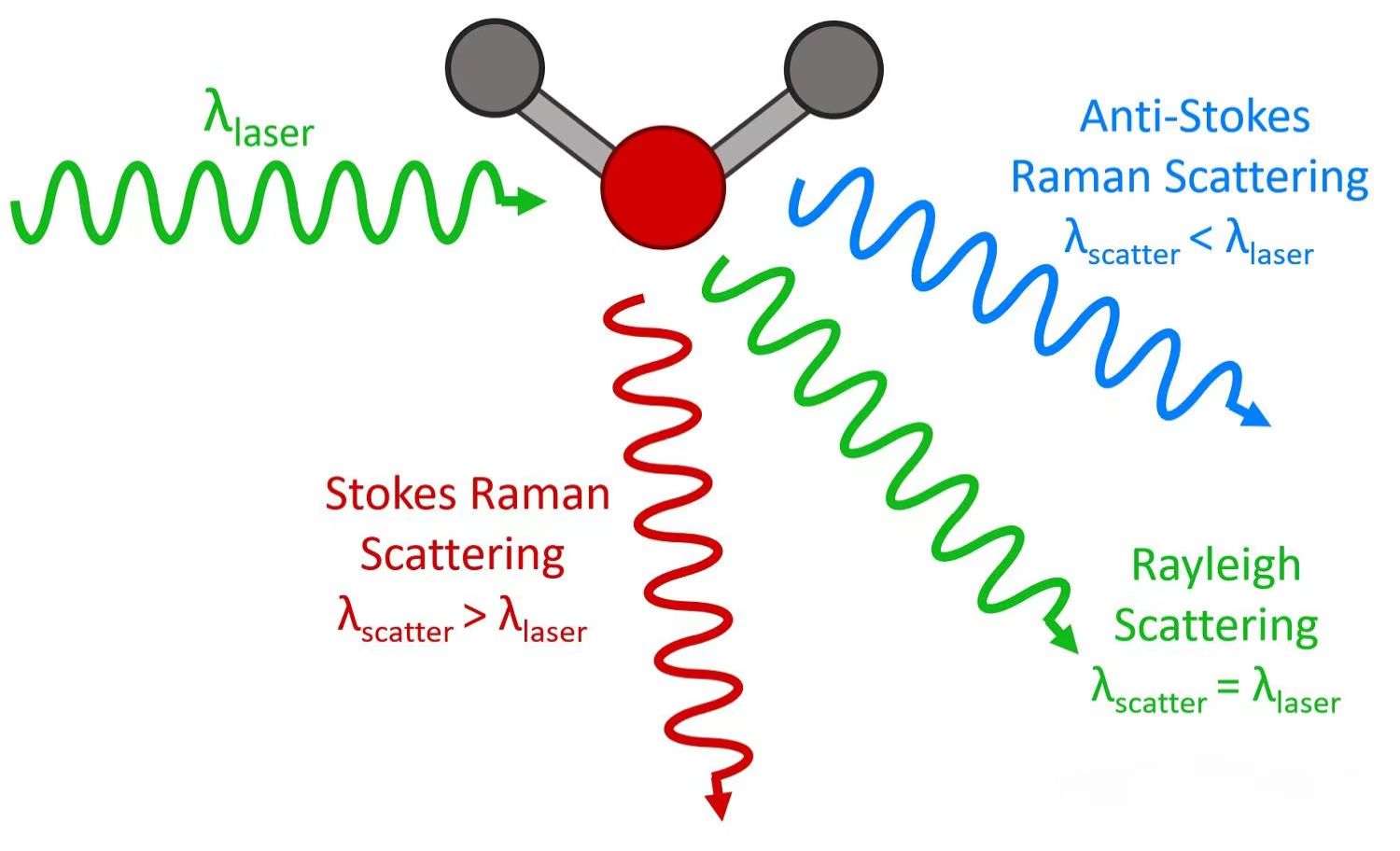
At present, DTS technology has been widely used in energy, transportation, environmental protection and other fields. In the field of energy, DTS can be used to monitor the temperature of oil and gas pipelines such as oil and gas Wells. In the field of transportation, DTS can be used to monitor the temperature of traffic facilities such as roads and Bridges, so as to alleviate and optimize traffic congestion. In the field of environmental protection, DTS can be used for temperature monitoring of environmental protection facilities such as sewage treatment plants and landfills, so as to achieve environmental monitoring and control.
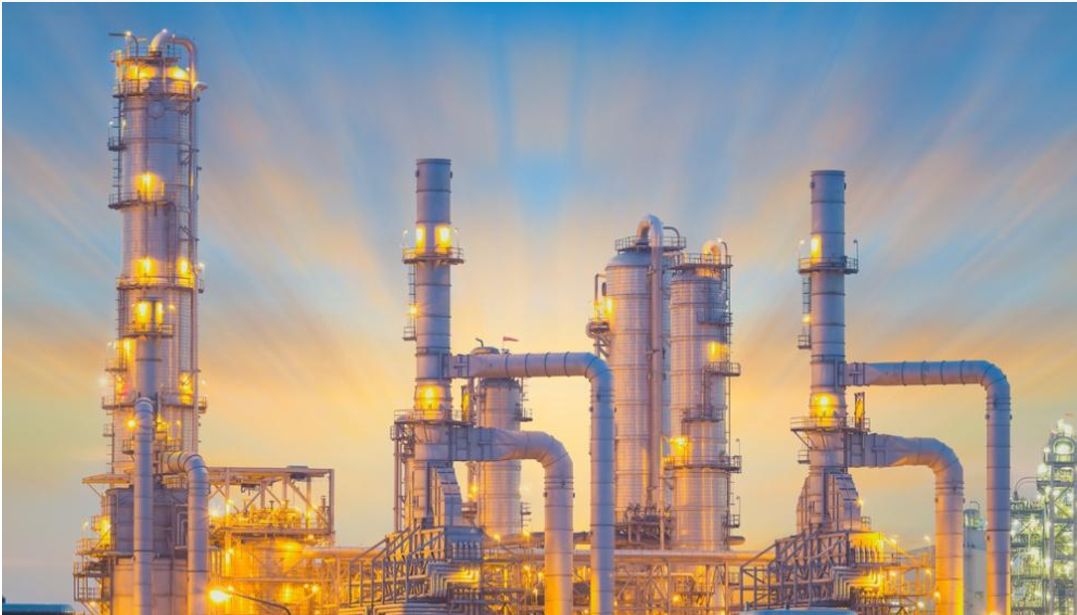
Distributed optical fiber temperature measurement technology is a very important technology, it has a wide range of applications, not only limited to fire warning, pipeline leak detection, power facility monitoring and other fields, but also can be used in environmental monitoring, geological exploration, industrial automation control and other fields, providing a more reliable guarantee for our life and work.
Distributed Temperature Sensing Cable
Typically DTS technology uses a standard telecoms fiber optic cable and specialised cables or sensing points are only required if measurements are required at temperatures greater than 100°C. The sensing fiber is typically based on multimode fibers for shorter ranges (up to 40km) and single mode fiber for long ranges (40-100km).
Fiber Optic Temperature Measurement Specification For DTS
Distributed temperature sensing systems can typically locate the temperature to within a distance of 1m (this is known as spatial resolution) with accuracy to within ±1°C and with a sensing resolution down to 0.01°C. However, there is an inverse relationship with measurement resolution, range and sampling time i.e. the temperature resolution degrades with range and improves the longer time you acquire data for a specific measurement.
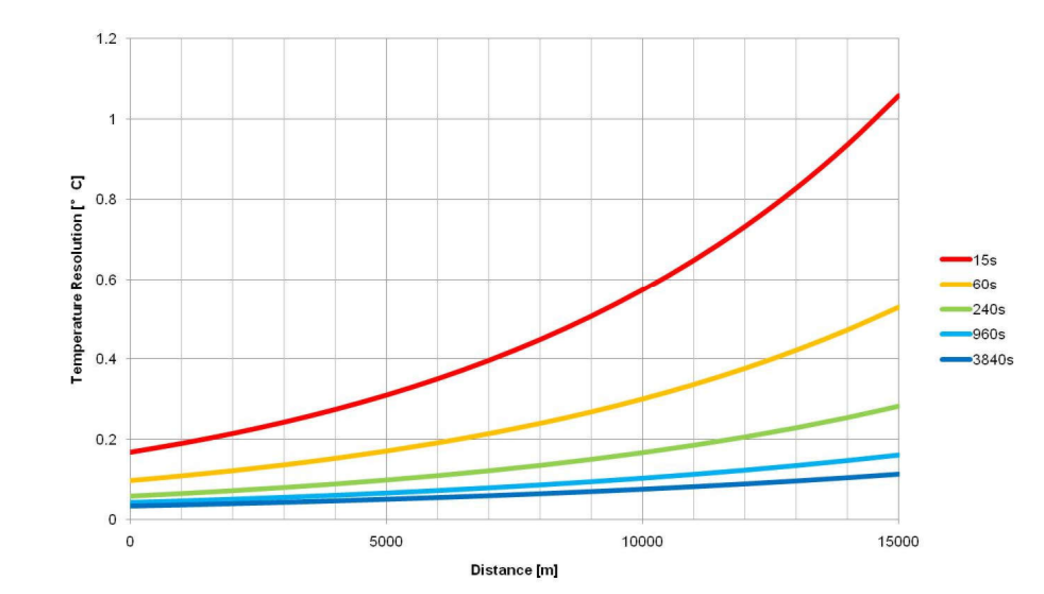
Distributed Temperature Sensing – Raman Measurement Principle
Fiber optics are made from doped quartz glass and when laser light is transmitted in a fiber optic an interaction occurs between the light particles (photons) and the electrons of the molecule. At a particular frequency in the electromagnetic spectrum (known as the Stokes and anti-Stokes bands), light scattering, also known as Raman scattering, occurs in the fiber optic. The intensity of the so-called anti-Stokes band is temperature-dependent, while the so-called Stokes band is practically independent of temperature. The local temperature of the optical fibre is derived from the ratio of the anti-Stokes and Stokes light intensities.
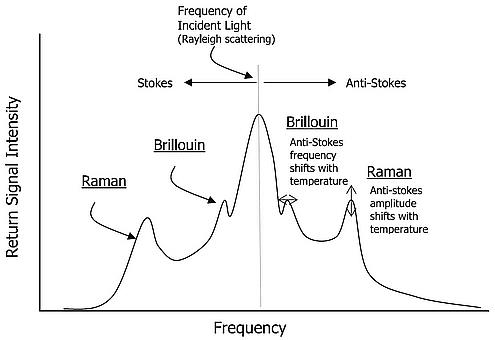
Measuring Principle – OTDR And OFDR Technology
There are two basic principles of measurement for distributed sensing technology, Optical Time Domain Reflectometry (OTDR) and Optical Frequency Domain Reflectometry (OFDR).
OTDR was developed more than 20 years ago and has become the industry standard for telecom loss measurements. The principle for OTDR is quite simple and is very similar to the time of flight measurement used for radar. Essentially a narrow laser pulse generated either by semiconductor or solid state lasers is sent into the fibre and the backscattered light is analysed. From the time it takes the backscattered light to return to the detection unit it is possible to locate the location of the temperature event.
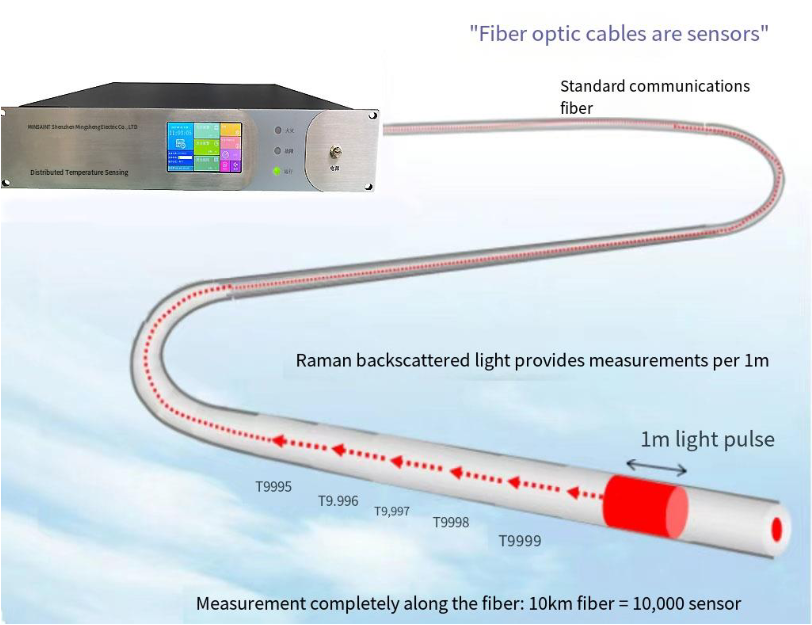
Alternative DTS evaluation units deploy the method of Optical Frequency Domain Reflectometry (OFDR). The OFDR system provides information on the local characteristic only when the backscatter signal detected during the entire measurement time is measured as a function of frequency in a complex fashion, and then subjected to Fourier transformation.
The vast majority of distributed temperature sensing systems available today is based on OTDR technology.
DTS can work in two ways: continuous wave (CW) and pulse reflection (OTDR). The continuous wave method is to measure the time delay and amplitude change of backscattered light by injecting continuous wave light signal into optical fiber, so as to obtain temperature information. The pulse reflection method is to measure the time delay and amplitude change of the reflected light by injecting the pulse light signal into the fiber, so as to obtain the temperature information.
system architecture
Tank temperature monitoring
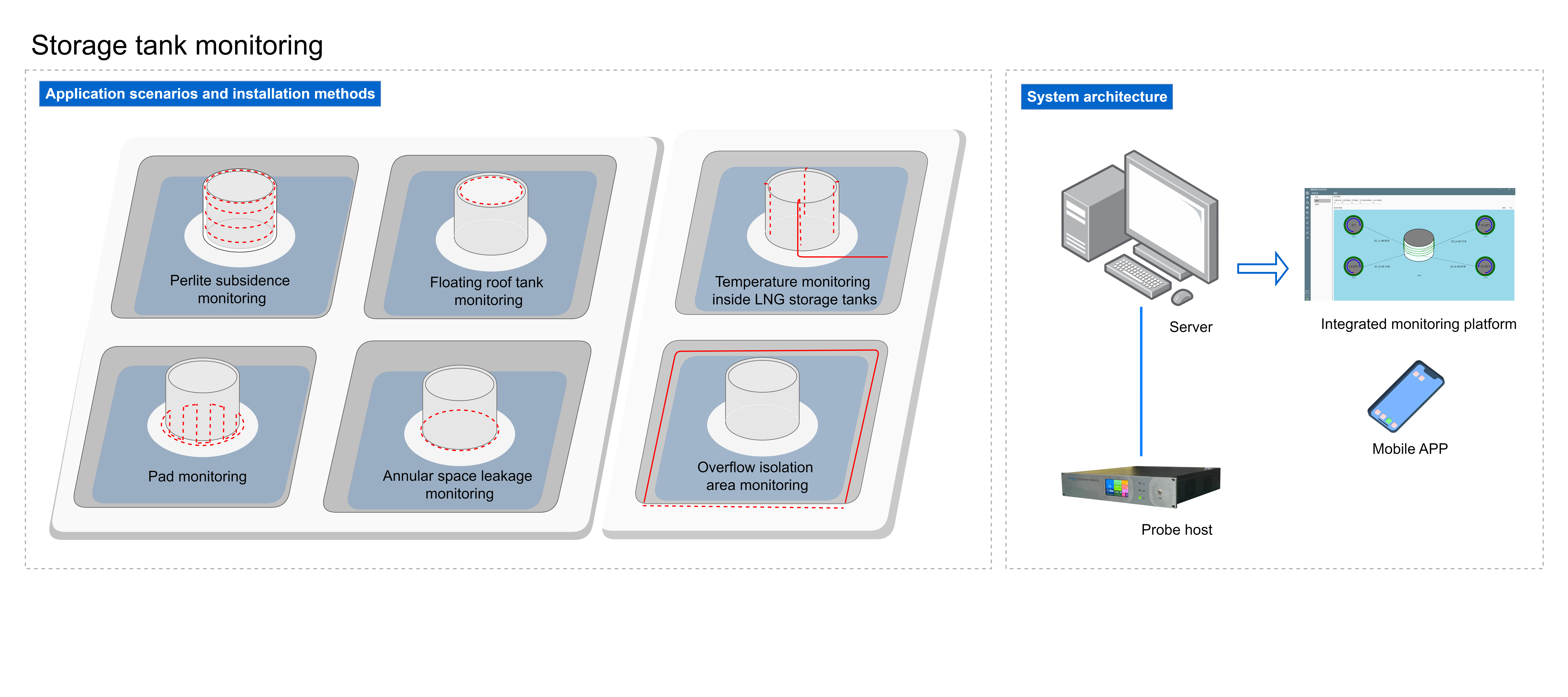
Pipeline leakage monitoring
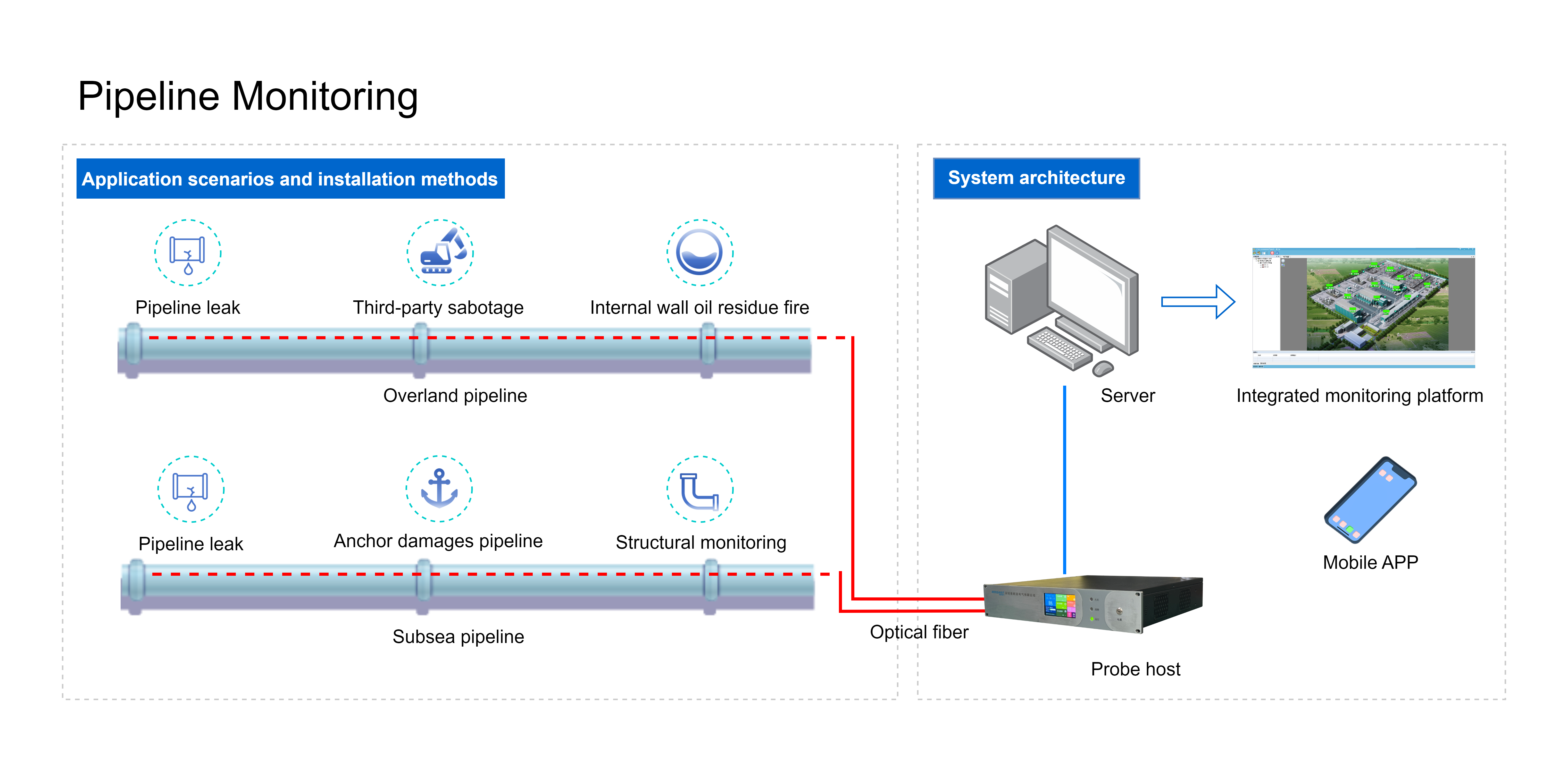
Advantages Of DTS Systems
1. Oil pipeline leakage detection: the purpose of oil pipeline leakage detection is realized by monitoring the temperature around the optical cable;
2. Abnormal alarm: When the detection temperature exceeds the set range, prompt alarm information and give operation suggestions
3.Differential fixed temperature alarm: alarm parameters support manual setting, output relay alarm signal and alarm positioning information, to achieve differential fixed temperature alarm
4.Alarm zone setting: the system can program the length of the alarm area and alarm point as a whole, which can be flexibly adjusted according to the scene situation;
5.Data analysis: historical data storage, query and analysis;
6.Remote access: The system can access industrial Ethernet to transmit data to management departments at all levels to achieve remote access.