Application analysis of distributed acoustic sensing in the oil and gas industry
Distributed acoustic sensing (DAS) is a fiber optic system based on Rayleigh scattering. Fiber optic cables act as sensing elements that measure, process, and analyze to deliver critical data, some examples of which we’ll explore below. DAS systems are capable of monitoring audio strain signals, sometimes over long distances and even in extreme environments. Sensing based on Rayleigh scattering is achieved by sending laser pulses along the fiber, which are scattered within the fiber so that the fiber acts as a distributed interferometer with a scale distance length approximately equal to the pulse length. The intensity of the reflected light is measured as a function of the time after the laser pulse is transmitted. The pulse travels and returns along the entire length of the fiber before the next laser pulse is sent along the fiber. The system is extremely sensitive to strain and temperature, so the readings are very accurate.
DAS is a technology that serves many applications to improve the quality and efficiency of production in the oil and gas industry. It is usually used for continuous monitoring of pipelines to check for interference, blockage, leakage and failure; For measuring private boundaries; In the application of well monitoring, real-time monitoring is very important for production. With the technology’s ability to work in challenging environments with extreme sensitivity and precision, its potential is unmatched, and here are eight outstanding reasons to invest in fiber optics in the oil and gas industry:
1.seismic streamer
Due to the vast area of the ocean and difficult conditions, it is difficult to monitor, so professional methods are needed to deliver accurate data. Seismic streamers are surface optical cables that monitor the ocean and are essential for understanding coastal and ocean dynamics, vulnerabilities at different time and spatial scales, and for interpreting impacts on global and local environments. A fundamental function of Marine monitoring in the oil and gas industry is to identify and locate the best areas to precisely target oil drilling. Ocean monitoring is needed now more than ever. The world’s oceans, coasts and Marine ecosystems are facing major changes and challenges as a result of increasing greenhouse gas emissions, coastal pollution, overfishing, coastal development and pressures from population growth. Oil drillers need to accurately monitor the ocean, determine the best drilling locations, and minimize the risk of harm to Marine ecosystems. And accurate monitoring of the ocean can prevent dangerous mistakes. Seismic streamers are sea-surface optical cables connected to hydrophones. Hydrophones have a network of sensors that can pick up the vibration response caused by heavy objects on land hitting the ground. The sensors can relay data to a seismic recording ship with a seismic streamer deployed. Seismic data is three-dimensional data collected at different times in the same area, and it is used to monitor each change over time, including fluid migration, saturation, pressure, and temperature changes. Distributed acoustic sensing (DAS) technology can convert ocean optical cables into seismometers. Fiber optic cables with Marine cable designs generate seismic images of the seabed and underlying geological structures. These images are generated by relaying echoes from signals reflected from the geophone and the hull. Seismic images obtained from DAS can be used to support geological hazard analysis and other underground exploration activities.
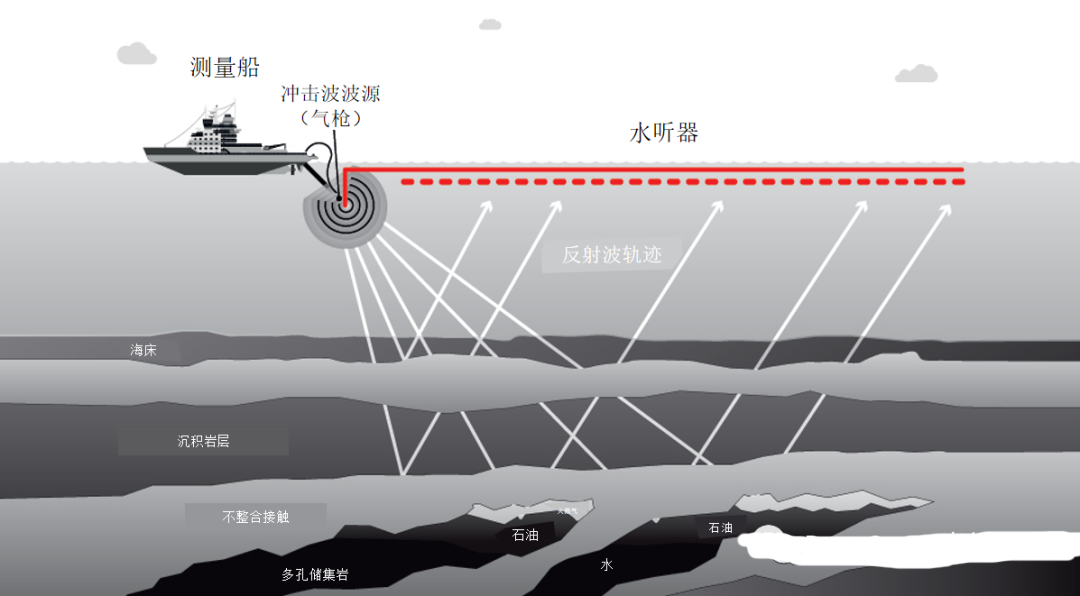
Figure 1 Offshore operation of seismic streamers
2.submarine optical cable
The oceans occupy most of the Earth’s surface and now face some of the toughest environmental challenges. So while exploring and monitoring the oceans is vital to our understanding of the world, it is also extremely difficult. In addition to the challenge of monitoring the environment, the sheer volume of the ocean floor presents another challenge: it requires equipment that can operate over a large area and be resilient (able to bounce back). As we learn more about the oceans, we can improve our understanding of Marine geology, offshore earthquakes, ocean currents, waves, sediment migration, and Marine mammals. In addition, by detecting changes in the Marine environment, we can eventually create a map of previously unknown fault systems and monitor seafloor dynamic processes. Submarine cables with distributed acoustic sensing (DAS) capabilities (also known as underwater or ocean floor cables) are fiber optic cables installed on the ocean floor that are capable of recording seismic data and transmitting the data to a recording vessel. Underwater fiber networks can predict waves, tsunamis and earthquakes by analyzing stress, strain and pressure in long-haul cables on the seabed. DAS uses fiber optics as sensors to turn undersea communication cables into powerful seismometers for surveying the ocean floor. DAS measurements have significant advantages over other measurement methods because they can assess the quality of the data in the Marine environment. In addition, submarine cables with distributed acoustic sensing capabilities (which can quickly transmit large amounts of information) are often thousands of kilometers long. Therefore, the ability to manufacture longer distance fiber optic metal protective tubes (FIMT, a protective element that enables fiber optic cables to operate in challenging harsh environments) is a critical advantage. NBG has recently made a major leap forward in the manufacturing of a longer continuous length of FIMT by constructing a new FIMT sheathing line up to 50 km long, which also makes the company’s advantage in the submarine cable industry even more prominent. But because
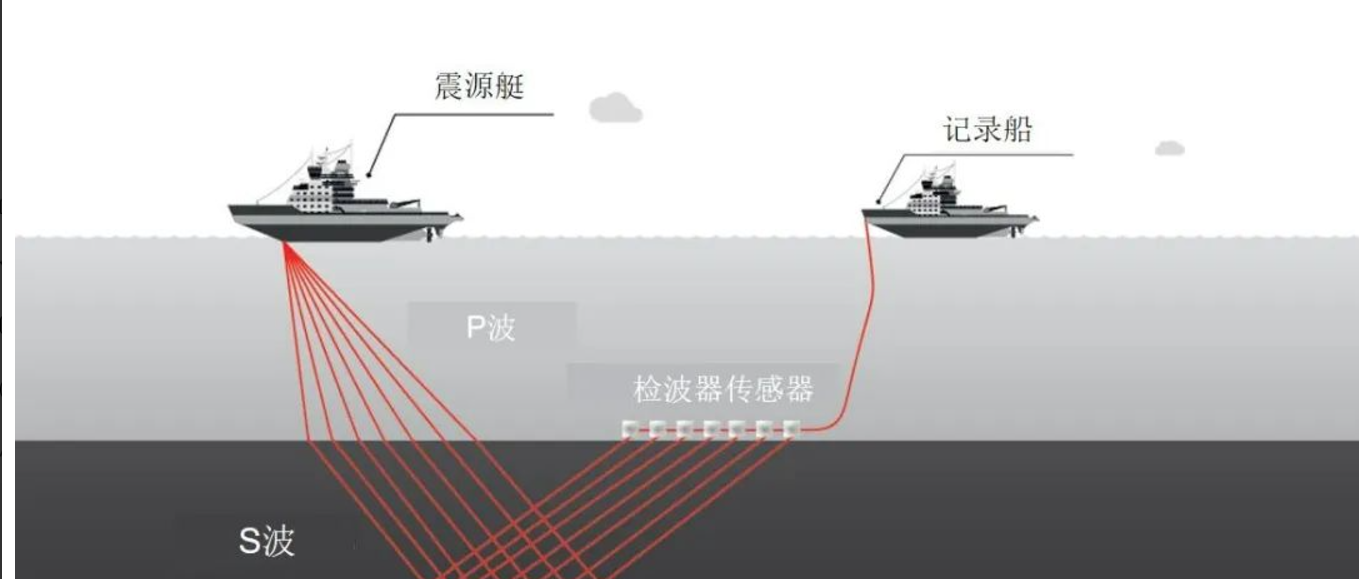
Figure 2 Submarine cable operation
3.Underground seismic survey
In the oil and gas industry, underground seismic surveys are used in the exploration phase of oil and gas development to determine the composition of subsurface materials. Therefore, for extraction projects, explorers need to know as much as possible about the nature of the subsurface components before drilling. Three main methods are commonly used to find hydrocarbons in the ground: geophysics, remote sensing, and field exploration. Choosing the best approach will help identify the most resource-rich areas, resulting in a strong return on investment. Changes in P-wave and S-wave velocities with depth can be assessed through downhole seismic surveys, where velocity data can be used to aid in seismogeologic responses at specific locations. Fiber optic sensors with distributed acoustic sensing are used as seismometers for the analysis of soil and rock mechanics and structures. The source is located on the surface, and the optical fiber sensor cable is located underground. The collected data is the propagation time of the P and S waves (measured by the optical fiber sensor cable) from the source located on the surface through the hole. Distributed acoustic sensing offers exceptional value by providing the most accurate data in real time.
The many benefits of underground seismic survey include:
1. Calculation of elastic modulus and geotechnical dynamic properties
2. Calculation of seismic site classification
3. Monitoring of faults, shear zones and voids
4. Diagnosing problem domains in two or three dimensions
5. Pre-grouting and post-grouting survey
6. Quality control during structural recovery
7. Quantitative evaluation of materials by seismic velocity analysis
8. Seismic shear and P-wave velocity sounding
9. The quality of rock or concrete is determined by estimating the dynamic coefficient of the material
10. Monitoring of bedrock faults and shear zones
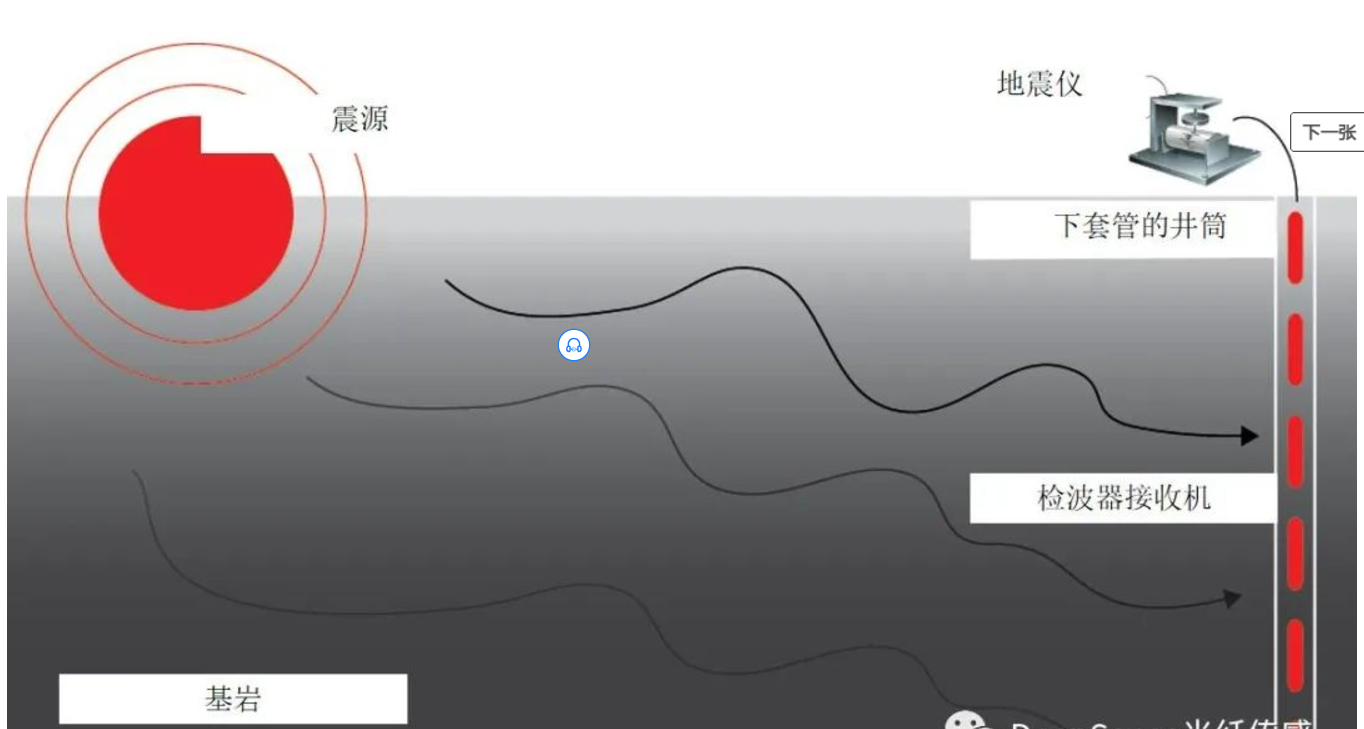
FIG. 3 Underground seismic survey
4.Sand detection
Many forms of sand control mechanical systems are not effective, resulting in poor sand inlet and production results. Sand production mainly affects pipeline design and overall operation in the following three aspects. First of all, the sand in the pipeline will aggravate the erosion of the pipeline; Secondly, the fluid velocity needs to be high enough to carry and remove sand particles in the flow line to prevent sand deposits from blocking the flow in the pipe; The final reason is that sand deposits in the pipe may prevent inhibiting chemicals (such as corrosion chemicals) from reaching the pipe wall, rendering the effect of the chemical ineffective. Ineffective sand control can result in compromised well integrity. The intrusion of sand bodies in the reservoir segment can lead to a decrease in hydrocarbon production. Overcoming this problem will greatly improve product quality while allowing it to be easier to maintain the life cycle of the application. Distributed acoustic sensing technology is the main candidate technology for downhole sand exploration. Optical fiber based acoustic sensing systems are used as sensing elements to monitor acoustic disturbances throughout the fiber using backscattered light injected into the fiber. Distributed acoustic sensing is capable of processing data in real time at the source, allowing applications in the following scenarios:
1. Monitoring the sand flow line
2. Monitoring the sand inlet in the production process
3. Increase hydrocarbon production
4. Inform and implement targeted containment operations
5. Control and manage sand-related risks during stimulation and production operations
6. Optimization of oil production
7. Assessing the reliability of sand control equipment during production can help improve future designs
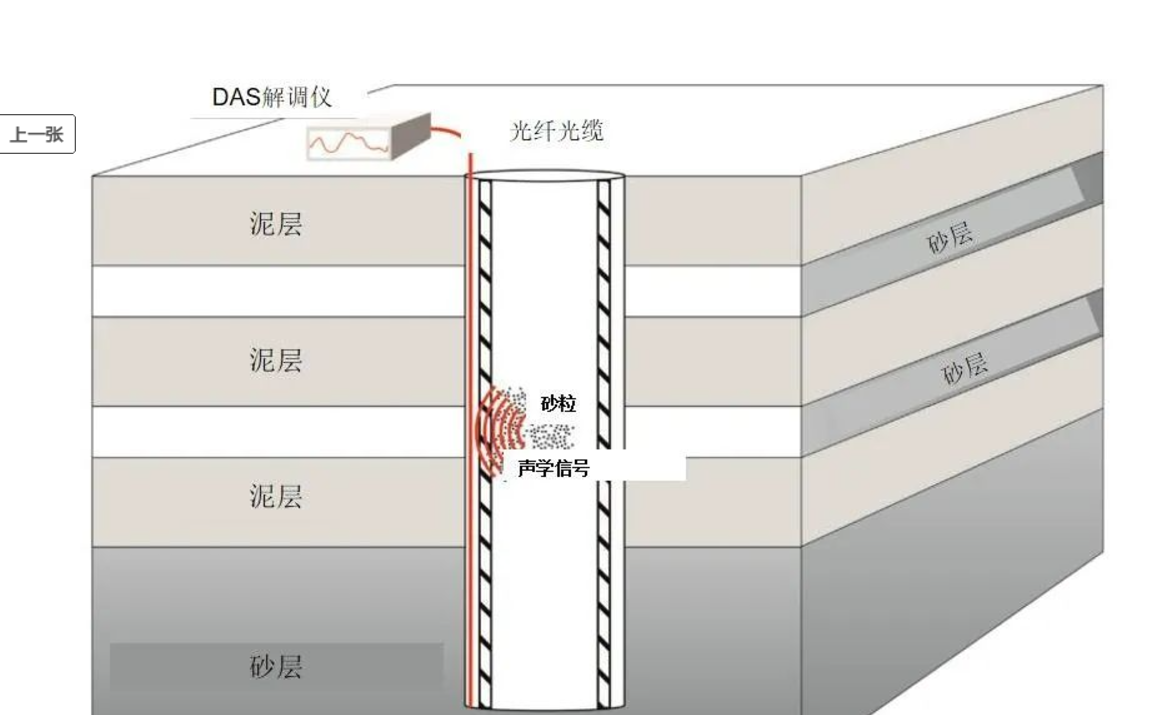
Figure 4 Sand detection
5.Perimeter Intrusion Detection System (PIDS)
The well is an asset of the oil and gas industry that needs to be protected to maintain well safety and production integrity. If an ineffective safety method is chosen, production at the site is vulnerable, resulting in a negative financial impact. If an intruder can be identified near the wellbore location, the integrity of production can be better ensured. Therefore, it is necessary to use an intrusion system that can withstand all conditions without degrading performance. When choosing an intrusion detection method, the factors that must be considered and prioritized are: detecting the intrusion before it attempts to enter, and alerting the control center at the earliest possible stage. Perimeter Intrusion Detection System (PIDS) is a generic term that covers a variety of techniques that are used to detect unwanted intruders trying to enter secure areas. PIDS are critical to any high-security site, making the organization’s work completely secure and reducing operational risk. PIDS do not replace surveillance cameras; they operate in conjunction with existing surveillance systems to provide real-time early intrusion detection. In addition, the technology is mainly passive and has strong anti-interference ability, robustness and resilience under electromagnetic interference or extreme weather conditions. Compared with traditional surveillance methods, optical fiber technology has many advantages. For example, a single detection unit that only needs to be buried in the ground (or mounted on a wall, fence) can provide fully scalable and robust security for areas of all sizes. In addition, fiber optic monitoring systems are a more cost-effective solution compared to competing technologies, and it offers a lower lifetime cost of ownership.
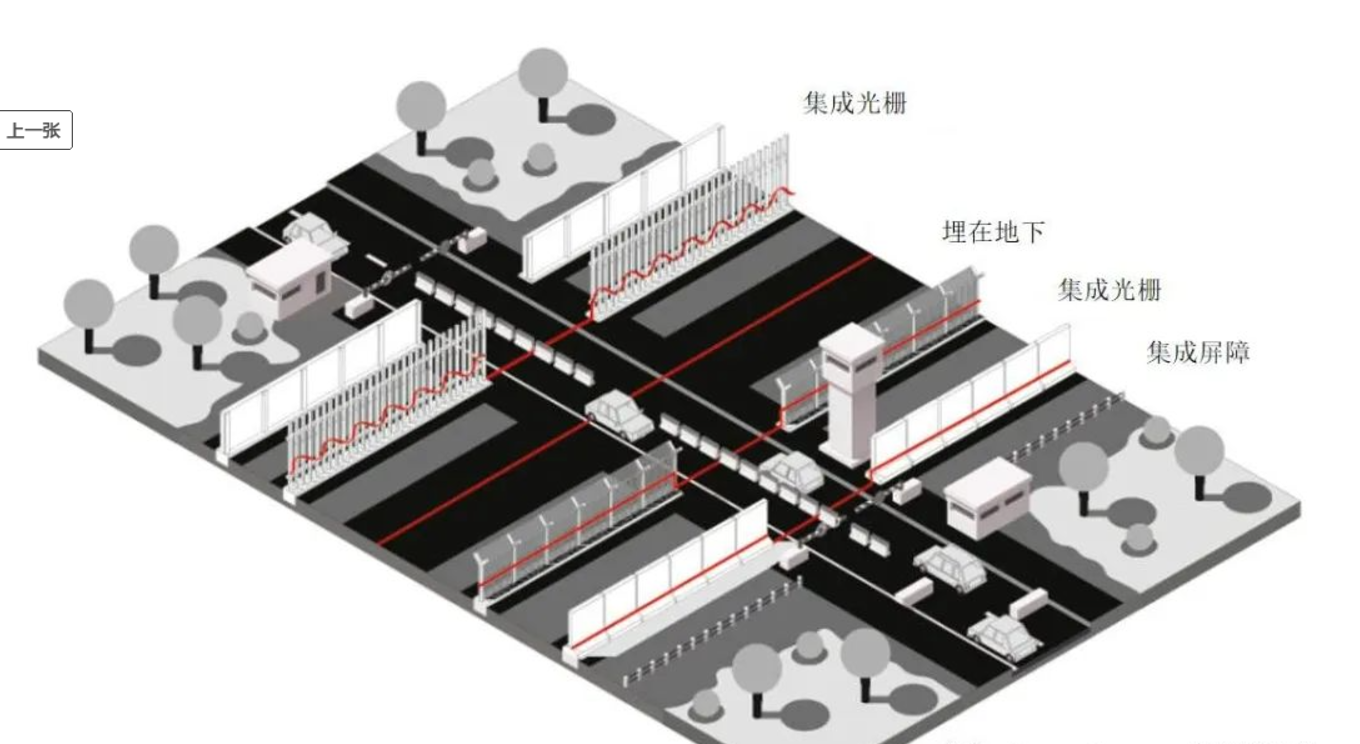
Figure 5 Intrusion monitoring system around wellbore
As perimeter intrusion detection systems are one of NBG’s core areas of expertise, the services it offers include:
1. Wellbore on-site monitoring solutions
2. Solutions of any length circumference
3. Future-proof technology that meets customer requirements
4. A software platform
5. A system that can be integrated with existing security system
6. Suitable for different terrain: soil, sand and gravel
6.crack monitoring
Fracking has been a viable method of drilling for natural gas above ground since 1940. Either way, it has only recently become popular due to the increased difficulty of finding natural resources underground. Conventional natural gas resources in the United States are running out, and fracking is still seen as an attractive and profitable method. A shaft is dug hundreds of metres underground and a horizontal hole is drilled into the oil and/or gas bearing rock. Next, high-performance pumps are used to transport fracturing fluids underground, penetrating rock formations and creating cracks. In this process, sand is also pumped into the rock formation (which prevents cracks from closing) so that oil or gas can be easily produced from the rock. If used correctly, fracking will help meet the demand for low-cost energy. In addition, the ability to accurately monitor well conditions will greatly reduce the likelihood of water contamination, which is one of the most pressing issues in hydraulic fracturing operations. Successful fiber deployment will also prevent the unintentional release of harmful and toxic substances, including greenhouse gases, into the environment. Fiber optic monitoring provides real-time and meaningful insights from data obtained from distributed temperature sensing (DTS) and distributed acoustic sensing (DAS). Operators with this insight will be able to gain a better and comprehensive understanding of subsurface conditions and make decisions and adjustments that will help determine the best fracture location and application performance. The result of implementing DAS and DTS is a more precise process that produces better results and reduces the possibility of operational inefficiencies and errors.
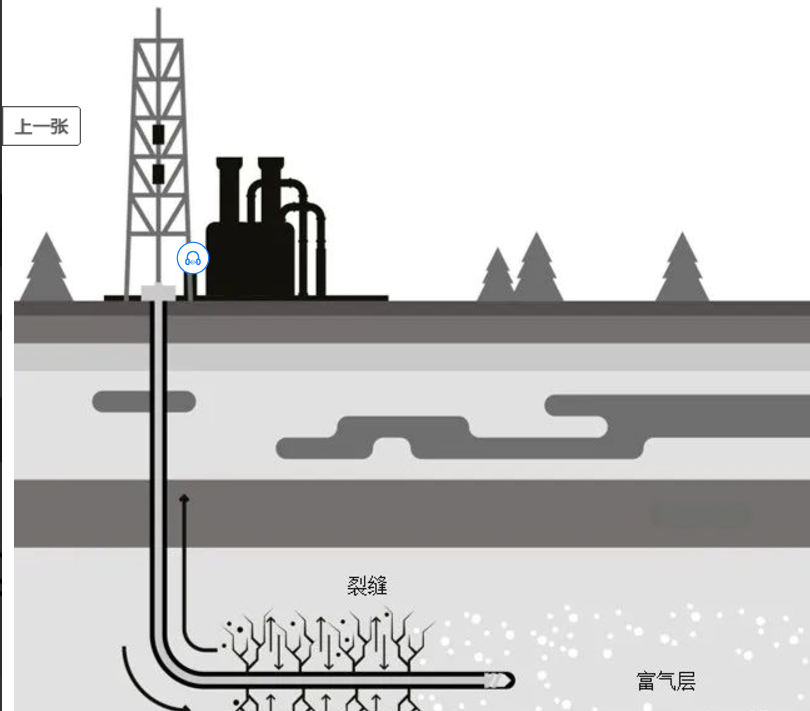
Figure 6 Crack monitoring
7.Fracturing shock during hydraulic fracturing
The pressure created by a well during hydraulic fracturing can affect nearby Wells (whether horizontal or vertical), which is known as “fracturing shock.” Although they vary in strength, connectivity between the two Wells can lead to pressure spikes and sand problems on the counteracting side, which can be disastrous for production. The following factors will determine the severity of a fracturing shock:
1.Well spacing: How close is the old well to the new well being fracked?
2. Formation characteristics: How permeable is the fluid (flowing formation) in the reservoir? Is there a crack in the well?
3. Pressure depletion: If the pressure drops, a pressure drop can be created for the new crack. The longer the drilling time, the better the fracturing effect.
4. Parent well: the longer the drilling time, the more obvious the fracturing effect, which is called the parent well. Counter the effects of “frac shock” by first communicating with the owner of the parent well and informing them of any work. In addition, operators should ensure that equipment has been modified to withstand fracturing shocks, reducing the chance of damage. Fiber optic technology plays the most important role in combating these effects. The most effective way to mitigate or even eliminate the effects of fracking is through mapping technology: fiber-optic microseismic monitoring. By monitoring well pressure, operators can assess the timing and severity of fracturing shocks. The monitoring of well production is also indicative of an imminent fracturing shock (the hallmark of an imminent fracturing shock is a rapid decline in production), and the increased volume of water indicates that fluids from newly fractured Wells are entering already producing Wells. Optical fiber is a tool that provides improved diagnostic methods. Distributed acoustic sensing (DAS) and even distributed temperature sensing (DTS) can measure critical data to determine the condition of a well. DAS provided important data on the strain response when the fracture interacts with the adjacent well, which was supported by fiber optic microseismic analysis, allowing the analysis to show the time series of microseismic events and reveal the fracture network. Microseismic analysis is a cost-effective solution that allows operators to obtain the necessary information.
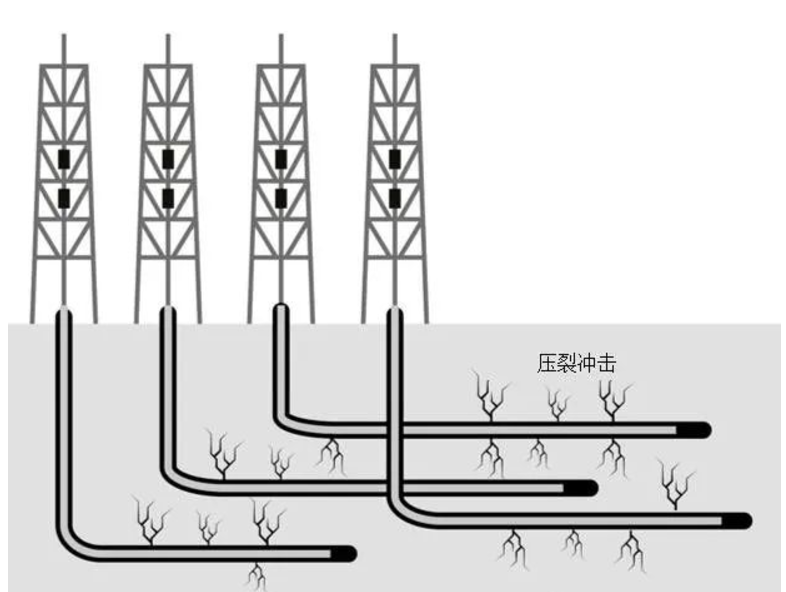
FIG. 7 Fracturing shock during hydraulic fracturing
8.inspection & coating
Pipeline monitoring is an important measure in midstream oil and gas applications to prevent costly spills that can have potentially catastrophic consequences for the environment, property and people. Optical fiber sensing technology represents the most efficient and reliable method; Distributed acoustic sensing (DAS) in pipeline monitoring ensures pipeline and product integrity throughout the downstream process through immediate leak monitoring and precise location of leak sources.
FIMT (Fiber optic Metal sheathing Wire) is ideal for pipeline monitoring because it can cover great distances, is resilient and durable in harsh conditions, requires little maintenance after field installation, and performs well in a variety of meteorological conditions. Being able to operate in harsh environments is an absolute prerequisite for heavy industries, such as the oil and gas industry, where processes are complex and involve large and heavy products, equipment and facilities. NBG’s Fiber Metal sheathed wire (FIMT) is the protective element that enables fiber optics to operate in some of the world’s harshest environments.
The optical fibers in the FIMT are used as sensors to monitor temperature and acoustic information in pipes up to hundreds of meters long. Using this technology to monitor pipelines, any disturbance caused by external influences, attempted theft, or by leaks will be detected immediately and located within meters of accuracy.
By using a fiber-optic monitoring system, other events in the pipeline can also be monitored, such as negative pressure waves (NPW), fluid shrinkage due to wax formation or hydrate formation, scrapers, pigs, and fluid buildup. DAS and DTS technologies can be implemented individually or within the same cable to provide comprehensive pipeline leak monitoring and continuous monitoring for onshore and offshore pipelines in all operating environments (fluid, gas and multiphase flows). Managing pipelines hundreds of meters long is an impossible task without the use of fiber optic monitoring. In addition, failure to identify a leak or the inability to monitor the exact location of a leak has significant property damage and environmental consequences.
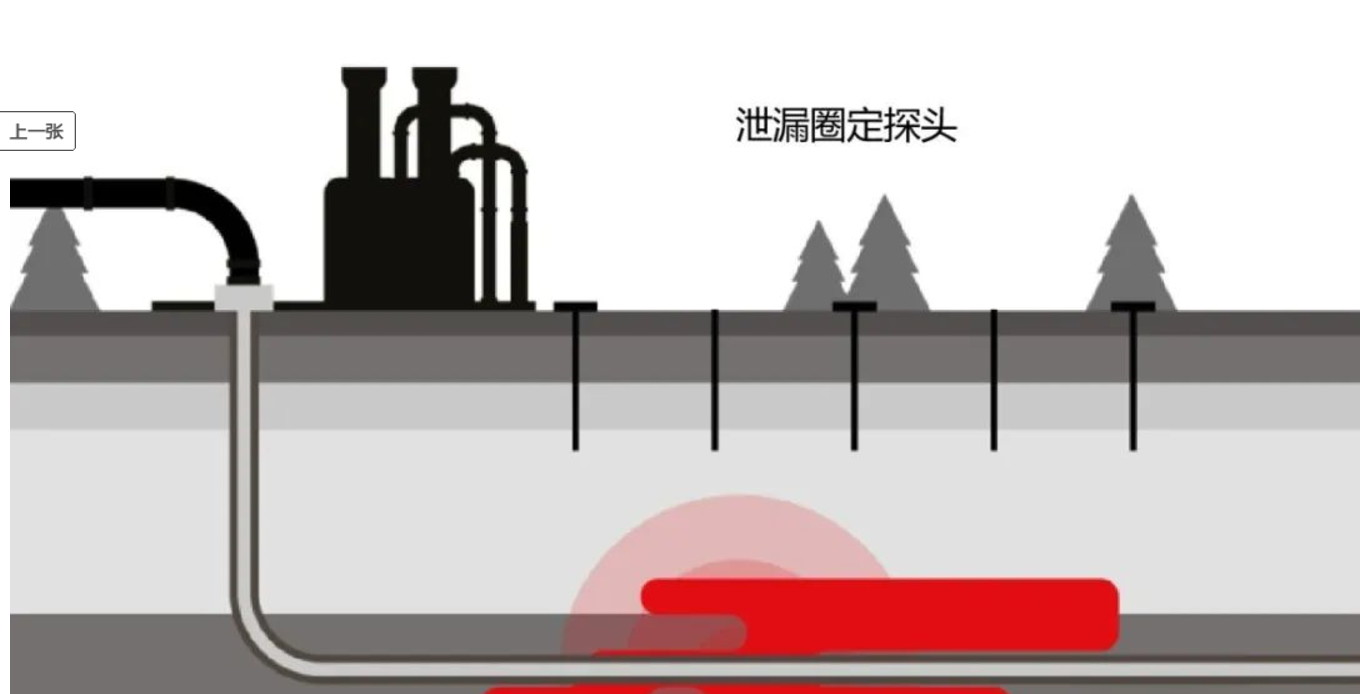
Figure 8 Pipeline monitoring